Firmy produkcyjne pomimo dużego poziomu automatyzacji wciąż potrzebują wykwalifikowanego personelu do obsługi maszyn i linii produkcyjnych. Z uwagi na złożoność procesów produkcyjnych wymagany jest personel o określonych kompetencjach i odpowiednio przeszkolony. Pomimo, iż często są to proste czynności, to jednak istotny jest tu czas wykonywania pojedynczych czynności, dlatego też Optymalizacja procesów biznesowych nabiera coraz większego znaczenia.
Wiele firm produkcyjnych dotyka niewystarczająca efektywność procesów produkcyjnych. Okazuje się, że problemem nie są maszyny, a ludzie, zmieniające się wolumeny zamówień, problemy z dostawą komponentów na czas i ich jakość, etc. Całość tworzy złożoną mapę powiązań, która ma bezpośredni wpływ na wydajność produkcji.
Poniżej przedstawiono kilka przykładów powiązań między działem produkcji a innymi jednostkami organizacyjnymi:
- Dział logistyki – wpływ na terminową dostawę produktów
- Dział planowania produkcji – wpływ na zaangażowanie zasobów ludzkich, obsadzenie maszyn, przeplanowanie zadań w przypadku awarii, przestojów, etc.
- Dział utrzymania ruchu – wsparcie w sprawnym usunięciu awarii
- Dział jakości – kontrola jakości dostaw oraz półproduktów
- Dział księgowości – rozliczanie dostaw komponentów, rozliczanie produkcji w toki, etc.
- Dział marketingu – planowane kampanie marketingowe a możliwości produkcyjne
Aby podnieść efektywność całego procesu produkcyjnego konieczne jest wprowadzanie zmian w funkcjonowaniu zarówno w Dziale produkcji, jak i w innych jednostkach w firmie. Można to osiągnąć poprzez optymalizację procesów (cały proces optymalizacji procesów został omówiony na stronie optymalizacja procesów biznesowych).
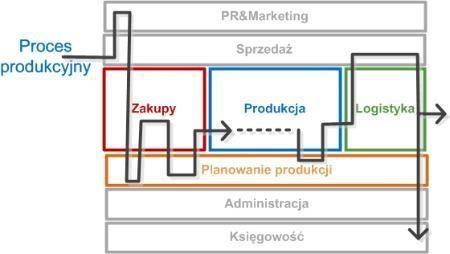
Posiadamy własną platformę do zakupu usług doradczych, gdzie można zakupić przykładowe mapy procesów dla obszaru produkcji. SPRADZ
Kiedy firmy zaczynają myśleć o optymalizacji procesów produkcyjnych?
- Dział produkcji rozrasta się rok do roku, ale nie wzrasta efektywność produkcji,
- optymalizacja procesów produkcyjnych staje się koniecznością z uwagi na brak zasobów,
- pojawia się więcej reklamacji od klientów niż w poprzednich latach,
- czas przezbrojeń oraz czas zatrzymania maszyn zaczyna mieć istotne znaczenie,
- skracano cykle produkcyjne technikami Lean ale mimo to nie osiągnięto oczekiwanej wydajności,
- nowi pracownicy mają problem szybką adaptacją do warunków w firmie
- Dział produkcji tworzy hermetyczne środowisko, w którym każda sugestia usprawnień natrafia na opór,
- istnieje słaba komunikacja między Działem produkcji a innymi działami w firmie,
- plany produkcyjne nie przystają do realnych możliwości zasobów produkcyjnych,
- duża rotacja pracowników w Dziale produkcji,
- duża zmienność zamówień od klientów,
- konkurencja oferuje niższe ceny przy podobnym poziomie jakości.
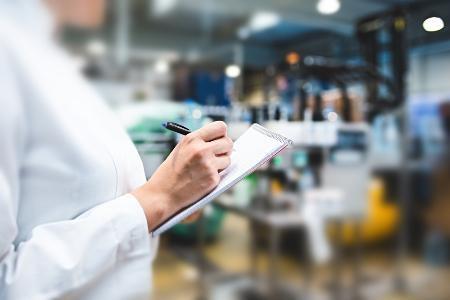
Wzrost efektywności można dokonać poprzez zmiany organizacyjne wewnątrz działu i na styku z innymi działami. Jednak aby wdrożyć takie usprawnienia konieczne jest posiadanie wiarygodnych danych – ile czasu zajmują poszczególne czynności i jakie są realne powiązania z procesem produkcyjnym….
Wzrost efektywności może osiągnąć kilkanaście % już w pierwszych miesiącach
Przykłady optymalizacji kosztów z wykorzystaniem pomiaru procesów
Wykorzystanie wyników z analizy i pomiaru procesów przez firmę produkcyjno-usługową do zmian organizacyjnych i struktury produktów.
- Zidentyfikowany problem początkowy: problem z rosnącymi kosztami Działu produkcji
- Zrealizowane działania przed pomiarem procesów
- Wprowadzenie procedur
- Problem na styku produkcji i działu wdrożeniowego
- Zdiagnozowany problem po pomiarze procesów
- Pomiar procesów ujawnił główne problemy w dziale (jakie? to już informacja poufna)
- Nadmierne zaangażowanie w proces sprzedaży przez inne działy
- Rozwiązanie
- Zostały opracowane rekomendacje związane ze zmianami na styku działów
- Opracowano mapy procesów wizualizujące wszystkie powiązania między działami
- Wdrożono nowe procedury
- Uszczelniono proces zakupów
- Zmieniono proces sprzedaży

Wynik z przeprowadzonej analizy i pomiaru procesów, wskazał że ponad 20% oszczędności da się z realizować z wykorzystaniem zmian poza działem produkcji. Zmiany w strukturze produktów pozwoliły zwiększyć rentowność o kolejne 10%
Wykorzystanie wyników pomiaru przez firmę produkcyjną do analizy wysokich kosztów produkcji produktów
-
- Zidentyfikowany problem początkowy: Rosnące koszty produkcji
- Poczynione działania:
- Zmiany organizacyjne w Dziale produkcji
- Zmiany w modelu zamówień od klientów
- Zmiany we współpracy z dostawcami
- Zdiagnozowane problemy po pomiarze procesów
- Identyfikacja całego łańcuch zależności niskiej efektywności produkcji
- Niska skuteczność planowania produkcji
- Brak współpracy Dział Handlowy – Dział planowania produkcji
- Działania technologów skupione na niewłaściwych działaniach
- Brak zaufania do pracy innych – działy „wolą sprawdzać pracę samodzielnie”, zamiast wymagać poprawy jakości od właściwych dostawców usług
- Brak osób odpowiedzialnych za procesy wspierające produkcję
- Rozwiązanie
- Utworzenie przebiegów procesów na nowo z uwzględnieniem precyzyjnego podziału zadań między działami
- Wprowadzenie instrukcji stanowiskowych
- Wdrożenie systemu do zarządzania przez cele
- Zwiększenie działań planowania produkcji
- Zaangażowanie Działu B+R w opracowanie tańszych rozwiązań
- Zmiana zakresu zadań Działu Kontroli Jakości
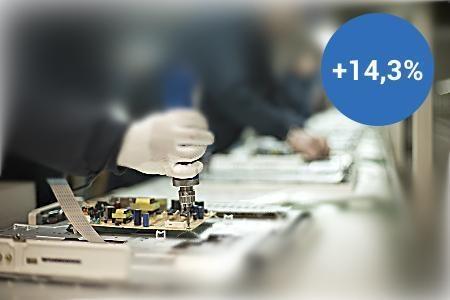
Wynik z przeprowadzonej analizy i pomiaru procesów pozwolił znaleźć ponad 15% oszczędności w Dziale produkcji poprzez usprawnienie działań w innych działach.
Wykorzystanie wyników pomiaru przez firmę produkcyjną do analizy wysokich kosztów produkcji produktów
-
- Zidentyfikowany problem początkowy: Podniesienie rentowności produkcji
- Poczynione działania:
- Zmiany organizacyjne w Dziale produkcji
- Skrócenie cyklu produkcyjnego
- Zmiany we współpracy z dostawcami
- Zmiany w dziale jakości uszczelniające dostawy komponentów i materiałów
- Zmiana parku maszynowego
- Skrócenie czasu przezbrojenia
- Wdrożenie systemu zarządzania przez cele
- Zdiagnozowane problemy po pomiarze procesów
- Identyfikacja całego łańcuch zależności niskiej efektywności produkcji
- Niska skuteczność planowania produkcji
- Działania kontroli jakości skupione na niewłaściwych elementach
- Działania technologów skupione na niewłaściwych działaniach
- Za wole usuwanie awarii
- Niewystarczający proces kontroli zmian
- Rozwiązanie
- Utworzenie przebiegów procesów na nowo z uwzględnieniem precyzyjnego podziału zadań między działami
- Zmiana zakresu zadań w ramach planowania produkcji
- Zmiana zakresu zadań Działu Kontroli Jakości
- Zmiana zakresu działań Działu Handlowego
- Zmiana zakresu zadań Działu wsparcia technicznego
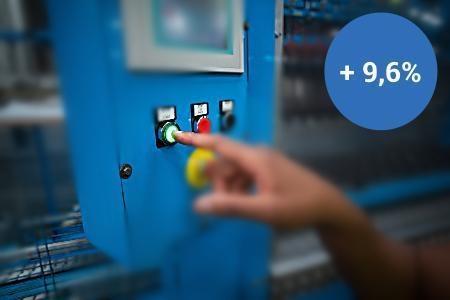
Wynik z przeprowadzonej analizy i pomiaru procesów pozwolił znaleźć blisko 10% oszczędności w Dziale produkcji . Projekt zwrócił się w 3 tyg.
Od czego zacząć?
Do każdego klienta podchodzimy indywidualnie. Poniżej przedstawiony został przykładowy schemat działań optymalizacyjnych:
1) Etap 1 – Analiza procesów
- Warsztaty z identyfikacji procesów
- Opracowanie Mapy czynności
- Pogłębiona analiza procesów / mapowanie
2) Etap 2 – Pomiar procesów
- Udostępnienie systemu do pomiaru procesów
- Nadzór nad pomiarem procesów przez cały okres trwania pomiaru
3) Etap 3 – Opracowanie rekomendacji
- Analizy porównawcze
- Analiza SWOT
- Opracowanie Planu usprawnień
4) Etap 4 – Wdrożenie usprawnień
Dlaczego warto nam zaufać?
- Mamy wieloletnie doświadczenie w analizie i pomiarze procesów biznesowych zrealizowaną w firmach z różnych branż
- Mamy świadomość wewnętrznych ograniczeń w firmach, dlatego proponujemy realne rozwiązania
- Posiadamy własną metodykę pomiaru procesów, która wskazuje najkosztowniejsze miejsca obsługi procesów
- Uzupełniamy metodyki Lean Management oraz SixSigma poprzez realne dane pomiarowe
- Łączymy wiedzę z menadżerskim doświadczeniem w prowadzeniu oraz zarządzaniu biznesem – dążenie do doskonałości nie jest celem samym w sobie, myślimy o kosztach i o realności wdrożenia rekomendacji z przeprowadzonej analizy procesów biznesowych
- Nasze doświadczenie pozwala nam szybko uchwycić specyfikę każdej firmy – nawet o najbardziej nietypowym działaniu.
- Przeprowadziliśmy kilkadziesiąt projektów optymalizacji procesów
- Przebadaliśmy ponad 600 tys. godzin pracy
- Przeanalizowaliśmy blisko 100o procesów
- Zwiększyliśmy efektywność o ponad 12 tyś osobodni
- Pomiar procesów o dane z ok 20 tyś. próbek danych (dla pomiaru 100 pracowników)